Are you are looking to protect a classic car chassis from corrosion with an impact resistant coating? As many classic car owners know, is important to protect the bare chassis from the elements. It is important to remove damaging rust before it is irreparable.
Promain‘s technical team would like to introduce the benefits of cold galvanising with Zinga over hot dip galvanising.
Risks of Hot Dip Galvanising Car Chassis’
The benefit of the galvanizing is that it will get the inside and outside of the frame. This ensures protection of all crevices, overlaps and tight corners.
Hot dip galvanising requires drain holes for the drainage of the molten zinc. A Land Rover or Range Rover chassis is quite a bit bigger and a bit heavier than many other classic cars. Depending on the model, some Range Rover’s chassis have lots of 1″ holes all over its 2 main sections. This allows the molten metal and hot gasses etc to dissipate evenly as the chassis is under immersion. This system of manufacture is not always feasible so hot dipping is not always possible.
Warp damage is a concern to classic car enthusiasts. Any air in spaces can potentially expand, distorting and weakening the frame.
The Benefits of Cold Galvanising Chassis’ With Zinga
Flexible Protection – Zinga caters for the torsion of the car chassis without risking brittleness of the coating.
Easy Application Available On Site – Zinga can be applied in the same way as paints.
Active Cathodic Protection – The film galvanising system Zinga (also called “Zinganisation“) shows comparable protection to hot dip galvanising and in some circumstances even superior protection (e.g. such as in immersion).
Suitable For Welding On Coated Steel – Since the Zinga is not in any way alloyed with the steel, there is no danger of zinc inclusion in the weld.
Car Chassis Keep Their Form During Application – Zinga is applied under ambient temperature and does not deform the structure. Zinga is applied under ambient temperature and does not deform the structure. With hot-dip galvanisation, deformation of the structure is possible due to the use of high temperatures of molten Zinc. There is also potential for hydrogen embrittlement within welds. This can lead to problems when structures are precise in a steel structure to form connections.
Introducing Zinga
Zinga Film Galvanising System is a single pack coating that contains 96% zinc to provide cathodic protection of ferrous metals. You can use Zinga as an alternative to hot-dip metallisation, as a primer in a duplex system (active and passive) or as a recharging system for hot-dip galvanisation or metallisation or zinganised surfaces.
With the ability to be applied on site, Zinga avoids the need for dismantling ferrous metal structures. It provides a grey matt, non toxic finish. Zinga conforms to ISO standard 3549 in regard to its zinc purity of 99.995% and to ATM standard A780 in regard to its use as a repair coating for hot-dip galvanisation. Zinga can be overcoated with a compatible paint.
How Does Zinga Cold Galvanising Work?
Cathodic protection arises from the anode, sacrificing itself in favour of the base metal. This allows the resulting flow of electrons to prevent the chemical reaction of the corrosion. This means you can guarantee the protection of your metal, even if the zinc layer after slight damage. When you use Zinga, the sacrificial rate is reduced dramatically after the zinc layer has oxidised, and the natural porosity have been filled with zinc salts.
Additionally, the zinc particles within the Zinga layer are protected by the ‘organic binder’ without negatively affecting the electrical conductivity of the metal. This allows Zinga to create nearly the same galvanic potential between the zinc and the steel as hot dip galvanising, but with a lower rate of zinc loss due to the fact that the binder acts as a sort of ‘corrosion inhibitor’ to the zinc.
Applying Zinga To A Car Chassis
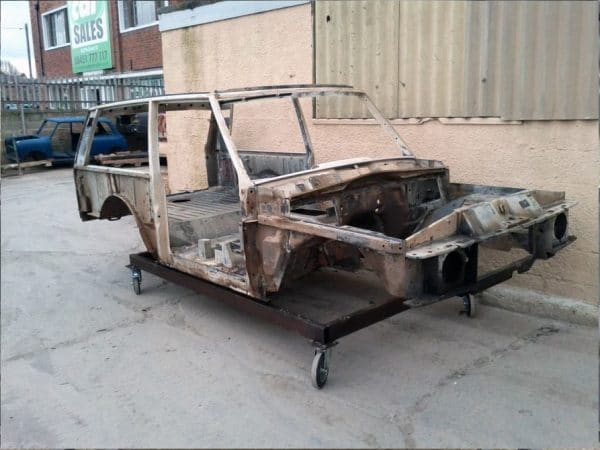
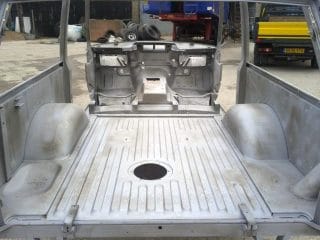
Degrease the bare chassis, preferably by steam cleaning. Afterwards, grit or slurry blast the metalwork to cleanliness degree of SA 2.5. The surface must be free from rust, grease, oil, paint, salt, dirt, mill scale and other contaminants.
After the bare chassis has had all paint and contaminants removed, Zinga 96% should be applied as soon as possible. The coating should have a thickness of to 60 microns when dry. Zinga can be applied by brush, roller, conventional spray gun or airless spray.
Priming and Topcoats
After the Zinga has fully cured, a suitable two pack primer can be applied to the framework. All conventional 2K automotive paints as well as basecoat or clear automotive coatings can overcoat Zinga.
Alternatively, Zinga Zingatarfree can be used as both the priming and topcoat. Apply one light coat of Zinga’s PU tar-free MIO in black. After 4 hours, apply a second heavy coat of Zinga Zingatarfree as per the product data sheet. This system should provide a minimum of 20 – 25 years of protection.
By cold galvanising a car body or chassis with Zinga, you can provide a great many years of protection against rust in any form on your car chassis.
Interested in finding more information about cold galvanisation via Zinga? View our extensive Zinga product range on our website here. Alternatively call our technical team on 01462 421333 to discuss your requirements.
Want to read more about cold galvanisation with Zinga? Read these: